Prof. Giuseppe Tomasso, Full Professor of Power Electronics, Electrical Drives and Machines, University of Cassino and Southern Lazio, Cassino, Italy; President, E-Lectra s.r.l., Greenergy s.r.l.; General Chair of the European PhD School on Power Electronics, Electrical Machines, Energy Control and Power Systems
New ways of thinking about the electricity grid
Smart charging solutions can serve as an essential tool in seamlessly integrating renewable energy sources into the power infrastruc-ture, while also optimizing the role of energy storage. This can obviously maximize utilization by synchronizing energy consumption with renewable energy generation peaks. But it can also be used to enhance grid stability, by dynamically adjusting energy demand, for example, by balancing charging over the electric vehicles (EVs) connected, and thus decreasing impacts on the grid. Extending this to the stationary storage systems in the infrastructure, can create an energy buffer and optimize not just the demand, but also the supply of energy over the daily cycle.
With the pending rollout of vehicle to grid (V2G) technology, EVs will not only consume electricity, but also be able to feed energy back into the grid, if needed. While this nominally increases the overall grid storage capacity, rather than using EV batteries to meet peaks of consumption, it would most likely be used in the form of more subtle grid services. For example, to respond rapidly to fluctuations, by using energy to stabilize frequency or support voltage levels. Obviously, for vehicle batteries, this could only use a small percentage of the capacity. But with today’s large vehicles, with capacities of 100 kWh and more, as well as the 100s of connected vehicles with lower capacity, grid support can be achieved without significantly impacting on range.
From the technical point of view, this is enabled by bidirectional power converters for charging stations and new communication protocols (such as the Combo CCS Type 2) and increasing numbers of vehicles that are capable of bidirectional power flow. The challenge now is to work out contracts between energy providers and EV owners. The advantage to the owner or user needs to be obvious, in the form of dis-counted or free energy volumes, for example, to overcome any concerns about reducing battery life (through using up charging cycles), or reducing range. For the energy providers, this is interesting because the cost of these discounts or energy volumes can still be a lot lower than running extra generation capacity to meet peaks in demand.
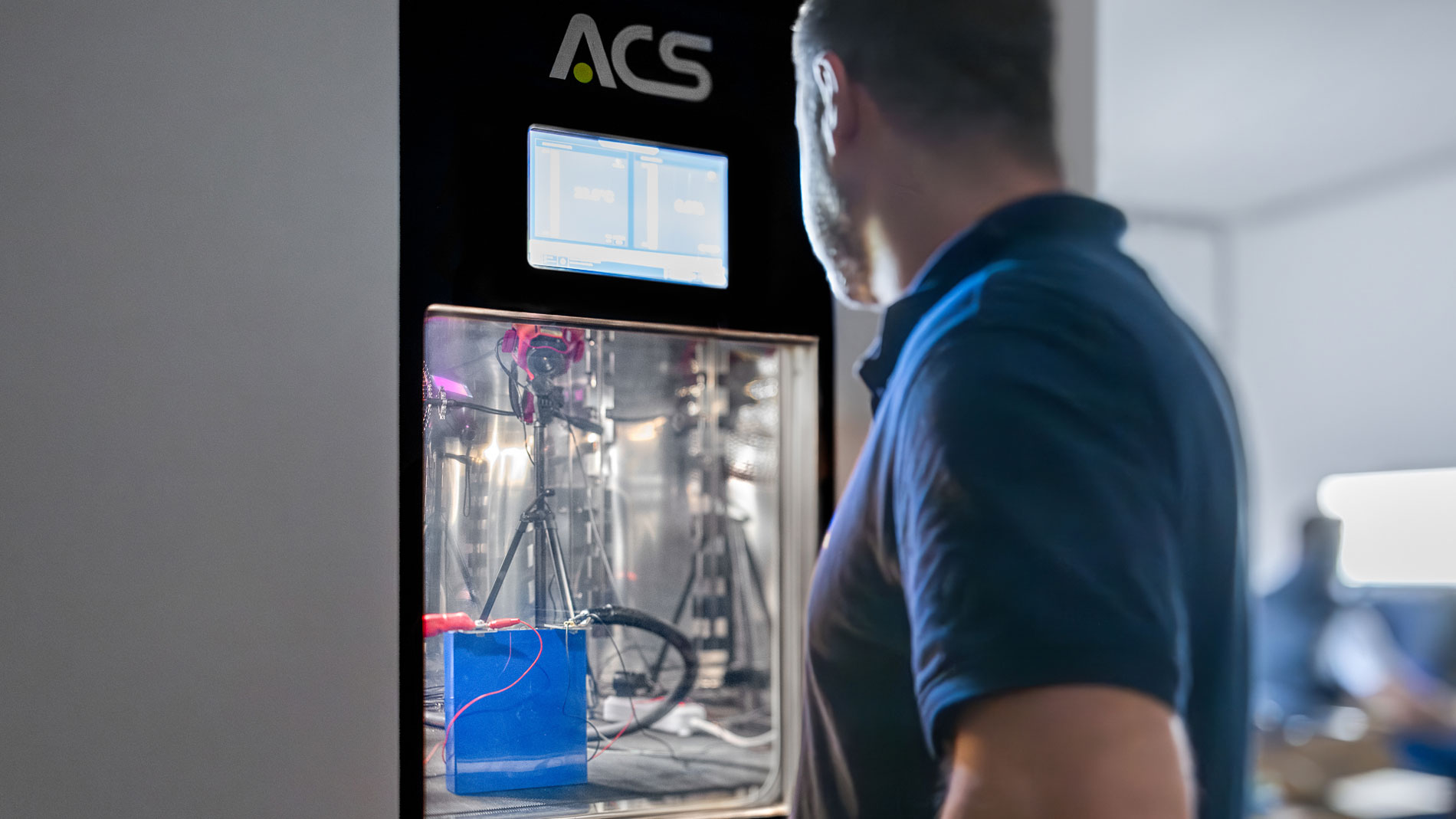
The battery management system as a differentiator for battery systems
The battery management system (BMS) is cen-tral to the technical success of V2G, but also to the more usual issues of battery performance, health, and safety. As such, it is probably the most important part of the battery system.
At the most immediate level, the BMS needs to serve the user’s needs, with information on status and likely range, and effective control of charging. But because the battery is the largest single cost in the power train of an EV, the BMS also needs to guarantee the health of the battery – to maximise the battery life. As the performance of cell chemistries converge, and the power densities of electric motors are already hard and expensive to improve, it is the BMS that can become an important differentiator for EV manufacturers. How it manages the storage can make the difference in how the vehicle performs, as well as on the life of the battery pack, and its safety.
To be effective, the BMS has to control voltage, current and temperature at the cell, module and pack levels. When it comes to safety, the BMS has to recognize potential problems early. For example, to activate the appropriate safety procedure as soon as it detects a problem in a single cell, or as soon as voltage, current, temperature, and vibration data predict an emerging issue across a module: recognizing a thermal runaway problem when it is al-ready affecting a module or the whole pack is too late.
Detailed control is also part of ensuring bal-anced charging, so every cell can reach its maximum storage, rather than stopping when the first cell reaches 100%, as well as ensuring battery life by distributing charging cycles across the battery, rather than exhausting some cells early.
Reusing traction batteries: second life or fundamental function
The BMS can also supply important data to is a crucial contributor to reducing the overall CO2 impact of EVs, by getting the greatest possible return on the environmental footprint involved in production. Usually after up to 2,000 charging cycles, the battery pack on an EV cannot guarantee the performance for the vehicle anymore. However, at 70 to 80% of its original capacity it is still useful for sta-tionary applications, and is probably good for another 2,000 to 3,000 charging cycles. This is interesting, for example, to energy providers building out their storage, not least because the cost is much lower than new.
The BMS plays a strategic role in providing comprehensive information about the battery pack: the state of health, whether there are crit-ical cells that need to be changed, and so on. As this market increases in importance, there is growing awareness among battery OEMs, who are making refurbishment easier, making reconnection possible, and not least enabling the BMS to continue to manage the battery in its second life. This is also the thinking be-hind the EU battery passport regulation, due to come into effect in 2027, which mandates battery data being available to enable reuse, or efficient recycling.
Second life for traction batteries is also fa-cilitating new business models. Such as the owner of an EV not having to buy a battery, but instead renting it (from an energy provider, for example) for the length of its “first” life. When it can no longer deliver the necessary vehicular performance, the energy provider can then use it in their stationary application. Second life might not just reduce the lifetime CO2 impact of a battery, but also improve attractiveness of EVs, by reducing battery costs.support the “second life” of an EV battery.
The changing face of battery safety
When it comes to safety, the BMS has an active role, as discussed above, in managing cell, module and pack temperature, and guarding against thermal runaway. But there are passive contributors to battery safety too, mostly in battery construction and chemistry. The balance that needs to be found is between increasing energy density, to reduce the space taken up by the battery, and the potential that tight packaging has for literally explosive reac-tions, for example, by short circuits caused by mechanical intrusions during vehicle impacts.
In part, this has to do with creating flame re-tardant barriers to limit thermal runaway, or at least to slow heat transfer for long enough that passengers can get clear of the vehicle. It is also the driver behind exploring more stable chemistries, such as lithium iron phosphate (LFP), rather than the more usual lithium nickel manganese cobalt oxides (NMC).
Safety is an area in flux as we gather more data on events in the real world. As in the case of air-craft safety, the regulations and certifications are likely to keep changing, in reaction to the emer-gence of new, unforeseeable incidents. There is a lot of very fast evolution in this area, that is likely to pick up momentum as the number of EVs increases, and we have better statistics.